Since the pandemic, it is not unusual to be in a business and see an empty shelf. The “empty shelf” has also carried over to the important materials cooperatives use to maintain electrical lines, build new services, and upgrade services.
At Todd-Wadena Electric Cooperative, there is no empty shelf. Our management team, Operations Department, and Member & Energy Services Department are actively planning and communicating to ensure our members’ electrical needs are met, even while material lead times are 100% greater than last year.
There is not just one situation affecting the global supply chain, but many:
Logistics and Freight
- Ocean freight congestion
- Trucking and small parcel freight:
» Shortages of truck drivers
» Increased operating costs
Raw Materials
- Russia-Ukraine conflict
- Growing demand for EVs and other markets
- Natural disasters
- COVID-19 lockdowns in China
- Chinese and Russian sanctions
Labor Challenges and Inflation
- Manufacturer space constraints
- 11 million job openings in the United States (as of the last business day of February)
- Wage pressures
Each of the departments at Todd-Wadena are working together to secure storm stock and other work plan needs. Last month, material needs for the 2023 Work Plan were ordered and await the 52-week lead time. It is not even the transformers and cable material items having longer lead times; items as small as our daily hardware have a lead time of over 20 weeks. We are thankful for the strong relationships we’ve built with the vendors and manufacturers we work with, especially during this challenging time.
Todd-Wadena Electric Cooperative’s team of employees is here for our members. If you are thinking about a new home, commercial developments, or upgrading electrical equipment – don’t wait to contact us. Please inform us of your plans as soon as possible so we can continue the no empty shelf!
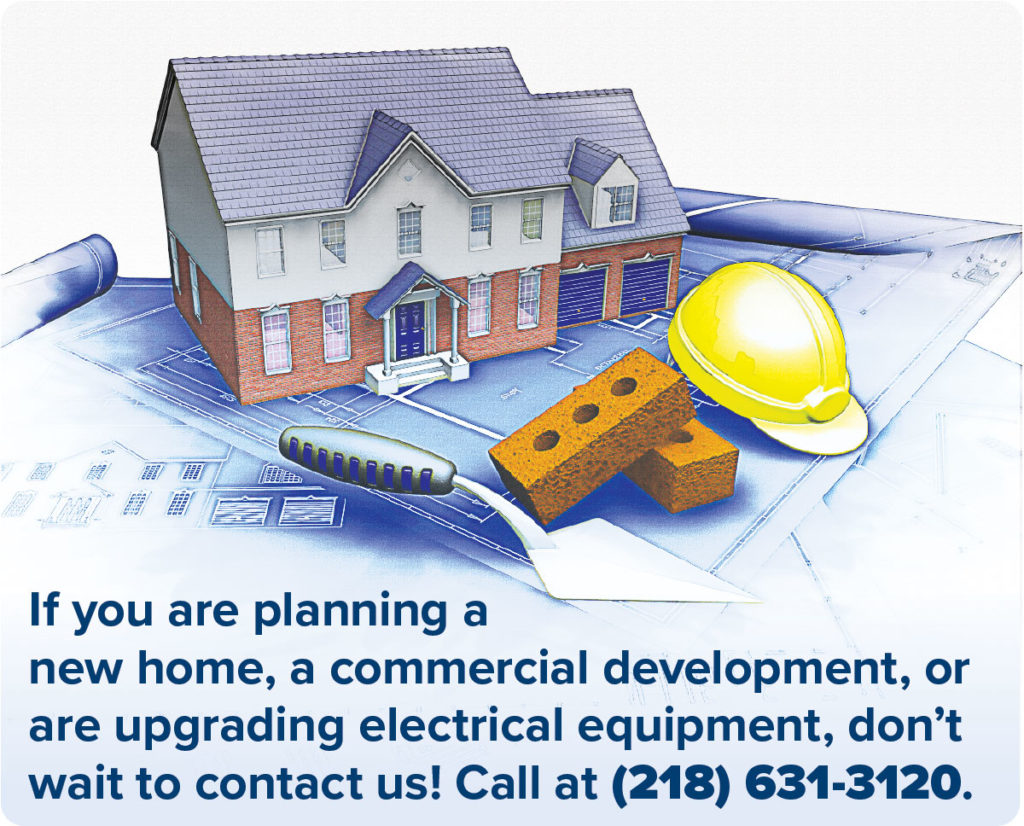